This website uses cookies for a better browsing experience.
If you agree to the use of cookies, please click the "Agree" button.
Please refer to the Privacy Policy regarding the use of cookies on this site.
This page describes dissimilar metal corrosion, which is one of the causes of wear on Oiles bearings.
When a combination of metal materials is exposed to an electrolyte solution (rainwater, seawater, etc.), battery action occurs and the material with the lower intrinsic potential selectively corrodes (Figure 1). The type of corrosion that occurs between materials with different intrinsic potentials is known as dissimilar metal corrosion (galvanic corrosion).
Figure 2 shows a list of the intrinsic potentials of individual materials in seawater for reference. Typically, the greater the difference in the potentials of the combined materials, the more likely is to occur dissimilar metal corrosion. The intrinsic potential of a material varies depending on the type of electrolyte solution, flow velocity of the solution, temperature, etc., so a material that is appropriate for the operating environment needs to be selected to prevent dissimilar metal corrosion.
Photo 1 shows an example of dissimilar metal corrosion in OILES 500. The solid lubricant embedded in OILES 500SP1-SL1 is graphite-based, which has a potential difference of about 900 mV with the carbon steel of the mating shaft in seawater. The example in Photo 1 was designed to be grease-filled, but rainwater has entered due to a broken seal and caused corrosion. This indicates that graphite (the solid lubricant) with a high intrinsic potential selectively corrodes carbon steel (the adjoining material) with a low intrinsic potential.
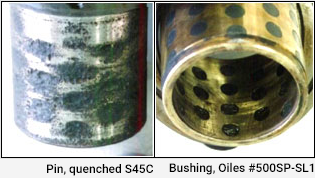
Photo 1 Example of dissimilar metal corrosion
Mating shaft: JIS S45C (carbon steel), hardened
Bearing: OILES 500SP1-SL1
The following methods can be used to prevent dissimilar metal corrosion.
- A design that avoids contact with moisture.
- Applying oil, grease, or some other lubricant to the contact surfaces of the bearing and mating material.
- Minimizing the potential difference between the bearing and mating material as much as possible.
Typically, a good rule of thumb is that the potential difference between combined materials should be 100 mV or less. - The most effective approach is to use materials that have no intrinsic potential.
Approaches include the use of plastic bearings or, in the case of bearings with an embedded solid lubricant, the use of a resin-based solid lubricant (e.g., SL464).
Source: (1) Japan Society of Corrosion Engineering, eds. 2000, Corrosion Engineering Handbook, p. 174